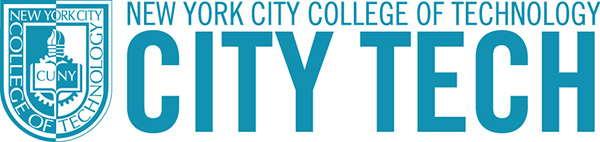
Publications and Research
Document Type
Article
Publication Date
2015
Abstract
The evolution of powder particle size, crystal structure, and surface chemistry was evaluated for micron scale NiO powders subjected to impact milling with commonly employed milling additives: methanol, Vertrel XF, and amorphous carbon. The effect of the different comminution protocols on sintered body microstructure was evaluated for high temperature sintering in inert atmosphere (N2). X-ray photoelectron spectroscopy showed that NiO powder surface chemistry is surprisingly sensitive to milling additive choice. In particular, the proportion of powder surface defect sites varied with additive, and methanol left an alcohol or alkoxy residue even after drying. Upon sintering to intermediate temperatures (1100 ℃), scanning electron microscopy (SEM) showed that slurry milled NiO powders exhibit hindered sintering behaviors. This effect was amplified for NiO milled with methanol, in which sub-500 nm grain sizes dominated even after sintering to 1100 ℃. Upon heating to high temperatures (1500 ℃), simultaneous differential scanning calorimetry/thermogravimetric analysis (DSC/TGA) showed that the powders containing carbon residues undergo carbothermal reduction, resulting in a melting transition between 1425 and 1454 ℃. Taken together, the results demonstrated that when processing metal oxide powders for advanced ceramics, the choice of milling additive is crucial as it exerts significant control over sintered body microstructure.
Comments
This article was originally published in the Journal of Advanced Ceramics, available at DOI: 10.1007/s40145-015-0147-z.
This article is distributed under the terms of the Creative Commons Attribution License which permits any use, distribution, and reproduction in any medium, provided the original author(s) and the source are credited.