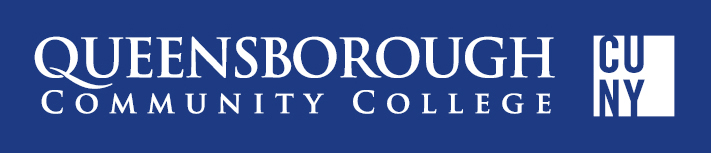
Publications and Research
Document Type
Article
Publication Date
2-3-2020
Abstract
Three dimensional (3D) printing as an advanced manufacturing technology is progressing to be established in the pharmaceutical industry to overcome the traditional manufacturing regime of ʹone size fits for allʹ. Using 3D printing, it is possible to design and develop complex dosage forms that can be suitable for tuning drug release. Polymers are the key materials that are necessary for 3D printing. Among all 3D printing processes, extrusion‐based (both fused deposition modeling (FDM) and pressure‐assisted microsyringe (PAM)) 3D printing is well researched for pharmaceutical manufacturing. It is important to understand which polymers are suitable for extrusion‐based 3D printing of pharmaceuticals and how their properties, as well as the behavior of polymer–active pharmaceutical ingredient (API) combinations, impact the printing process. Especially, understanding the rheology of the polymer and API–polymer mixtures is necessary for successful 3D printing of dosage forms or printed structures. This review has summarized a holistic materials–process perspective for polymers on extrusion‐based 3D printing. The main focus herein will be both FDM and PAM 3D printing processes. It elaborates the discussion on the comparison of 3D printing with the traditional direct compression process, the necessity of rheology, and the characterization techniques required for the printed structure, drug, and excipients. The current technological challenges, regulatory aspects, and the direction toward which the technology is moving, especially for personalized pharmaceuticals and multi‐drug printing, are also briefly discussed.
Comments
This article was originally published in Pharmaceutics, available at doi:10.3390/pharmaceutics12020124.
This article is an open access article distributed under the terms and conditions of the Creative Commons Attribution (CC BY) license (http://creativecommons.org/licenses/by/4.0/).